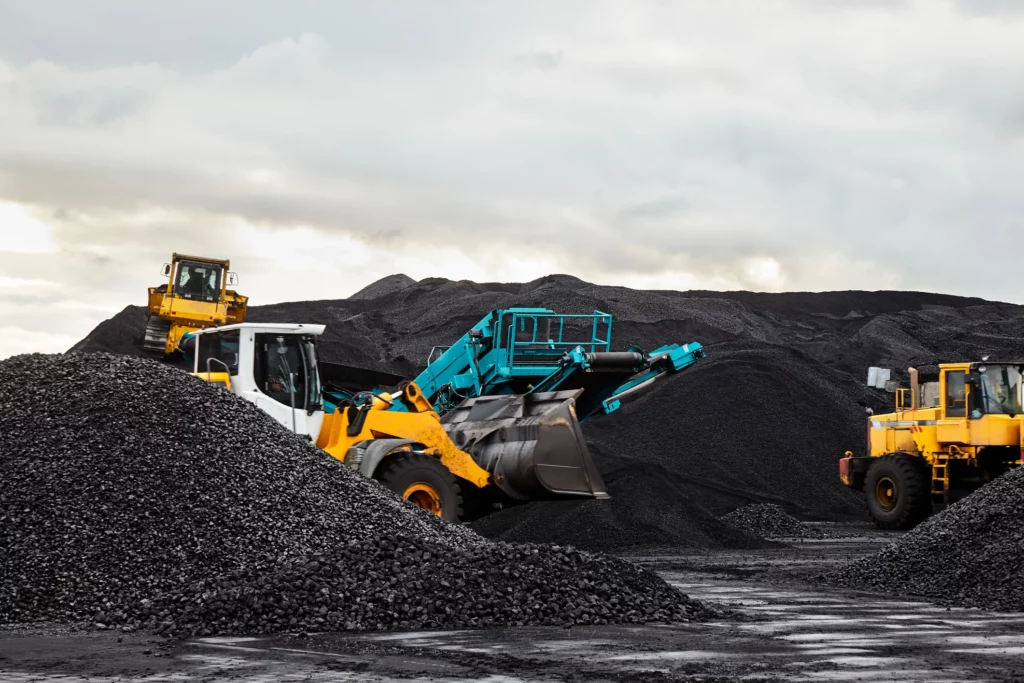
Unearthing Wealth: Iron Ore Mining
Among the many minerals and metals that these firms extract, iron ore holds a special place due to its widespread use in manufacturing and construction. Iron ore is the primary ingredient in steel production, a material that forms the backbone of modern infrastructure.
Companies engaged in iron ore mining are crucial for sustaining the global demand for steel. These operations involve the extraction of iron-rich rock and the processing of it into iron ore pellets, which are then used in steel mills worldwide. Key players in this sector include Rio Tinto and BHP Group, among others, as they deal primarily in iron ore extraction.
The World of Mining Companies
Mining companies play a pivotal role in the world’s economy. They are responsible for the extraction of various essential resources, including minerals, metals, and energy sources. These raw materials are the building blocks of modern society, powering industries ranging from manufacturing to technology.
The mining industry is vast and diverse, encompassing a wide range of materials and operations. From precious metals like gold and silver to industrial staples like coal, copper, and iron ore, these organizations are essential to ensure a steady supply of these resources. Their activities touch upon nearly every aspect of our daily lives.
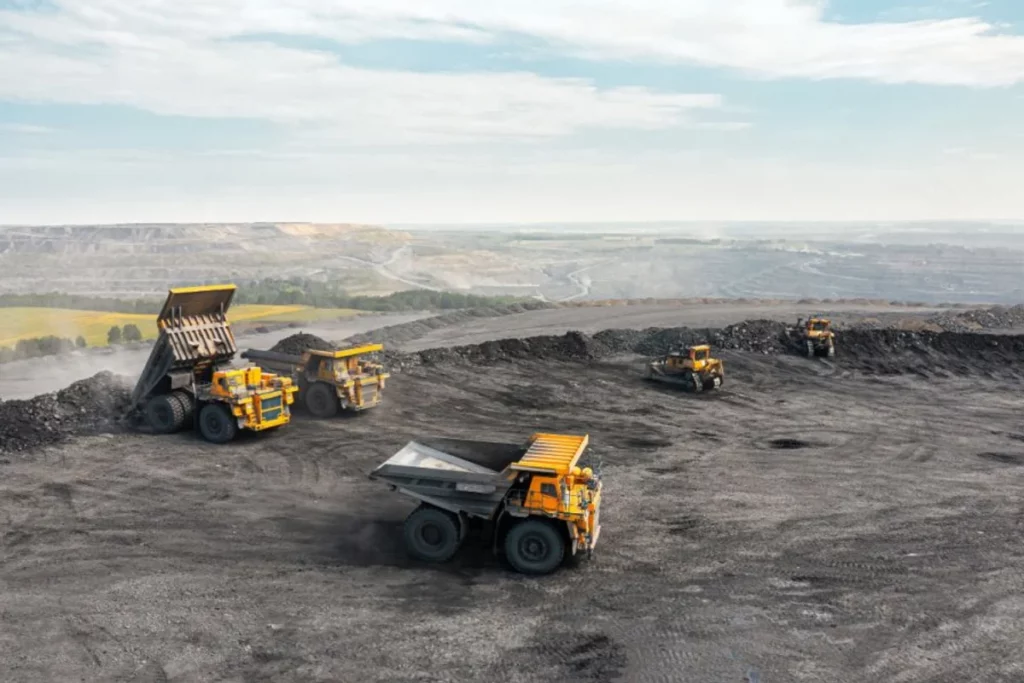
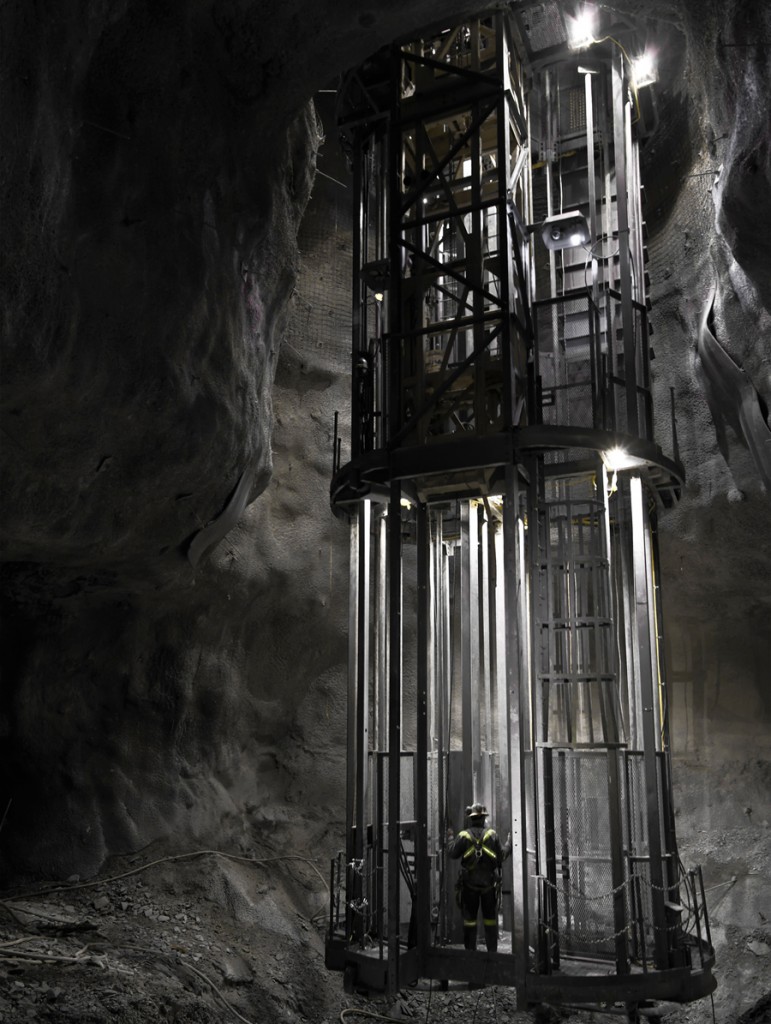
Sustainability: A Growing Concern
While these mining companies play a crucial role in meeting the world’s demand for resources, their activities can also have a significant impact on the environment. As a result, sustainability has become a growing concern within the sector. These firms are increasingly focusing on responsible practices to mitigate their environmental footprint and ensure the well-being of the communities where they operate.
The team at Writepaper comprises experts in various fields of study, guaranteeing that your essay will be written by someone with relevant knowledge and expertise. This results in essays that are not only well-written but also informative and insightful. The writers at Writepaper are dedicated to helping students succeed academically by providing top-notch essays that can serve as valuable learning resources.
One notable example of an organization that prioritizes sustainability is Wheaton Precious Metals. This firm specializes in streaming, which involves providing financing to mining organizations in exchange for a share of their future precious metal production. Wheaton Precious Metals ensures that its partner organizations adhere to high environmental and social standards.
Hecla Mining Company is another organization that emphasizes sustainability. Hecla operates mines in the United States and produces silver, gold, and other metals. It is committed to responsible mining practices and environmental stewardship, making it a leader in sustainable mining.
Top Mining Players: Leaders in the Industry
The mining industry is fiercely competitive, but a few organizations stand out as top producers, commanding the lion’s share of the market. These firms are not only leaders in terms of production but also have substantial market cap and mining assets. Let’s take a closer look at some of the prominent players in the world.
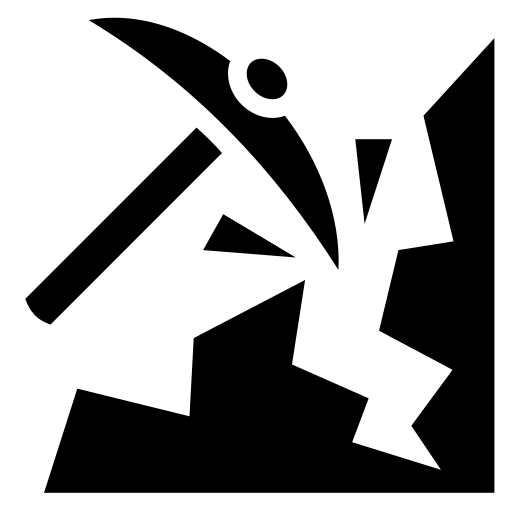
BHP Group
BHP Group is one of the world’s largest mining company. With a diversified portfolio that includes iron ore, copper, coal, and more, BHP operates on a global scale. Its market cap and mining assets make it a heavyweight in the industry.
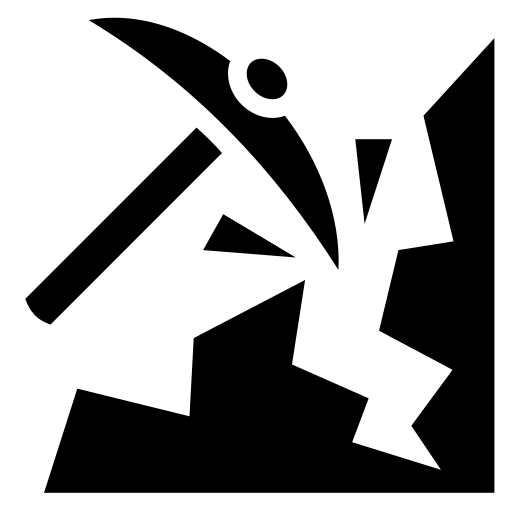
Rio Tinto
Rio Tinto is another global mining company, specializing in iron ore, aluminum, copper, and other metals. It has a significant presence in mainland China and South America, making it a key player in the sector.
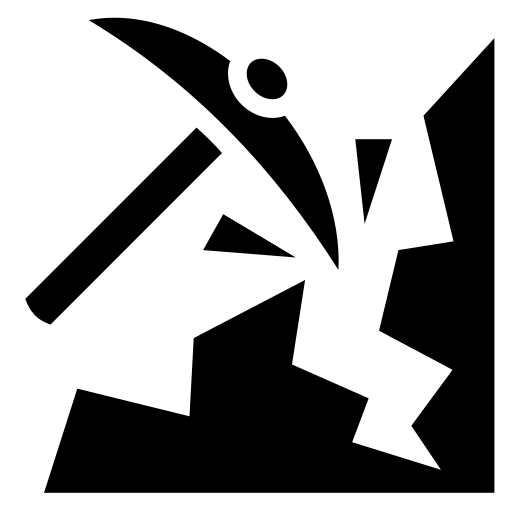
Cleveland-Cliffs
Cleveland-Cliffs is a leading producer of iron ore and metallurgical coal in North America. It focuses primarily on the production of raw materials essential for the steel industry.
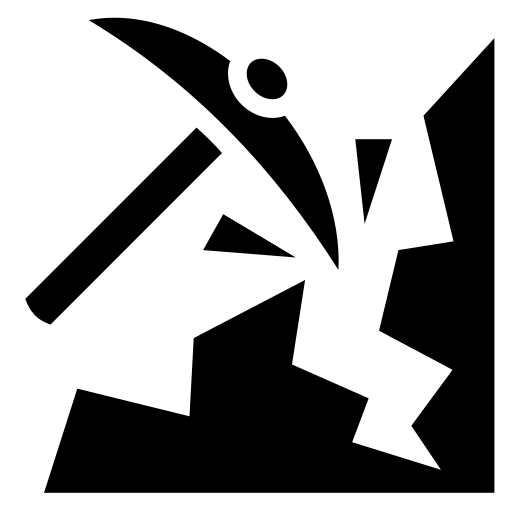
Anglo American
Anglo American is a diversified mining company with operations spanning various commodities, including platinum group metals, copper, and diamonds. Its global presence contributes to its prominence in the industry.
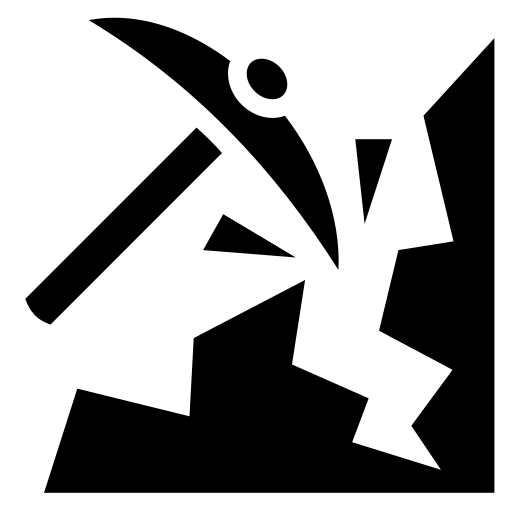
Glencore plc
Glencore plc is a major mining company and trading of commodities, including coal, copper, zinc, and nickel. Its reach extends across the globe, making it a significant force in the mining world.
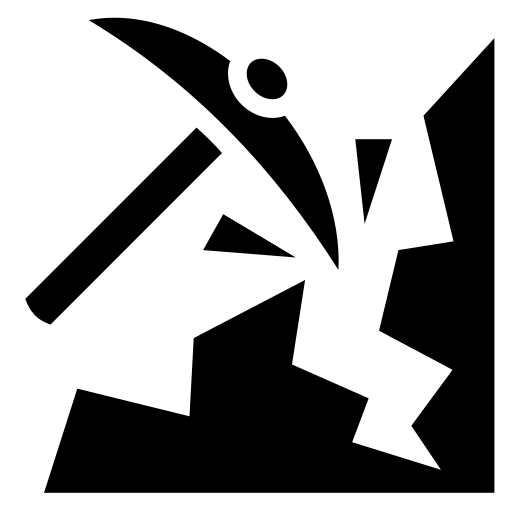
Artemis Gold
Its chief executive has raised $385m from a syndicate of Canadian banks at 4.8% and its chief operating officer has final permits to roll-out diesel trucks and a new gold mine in British Colombia, buying $105,261 at C$4.80.
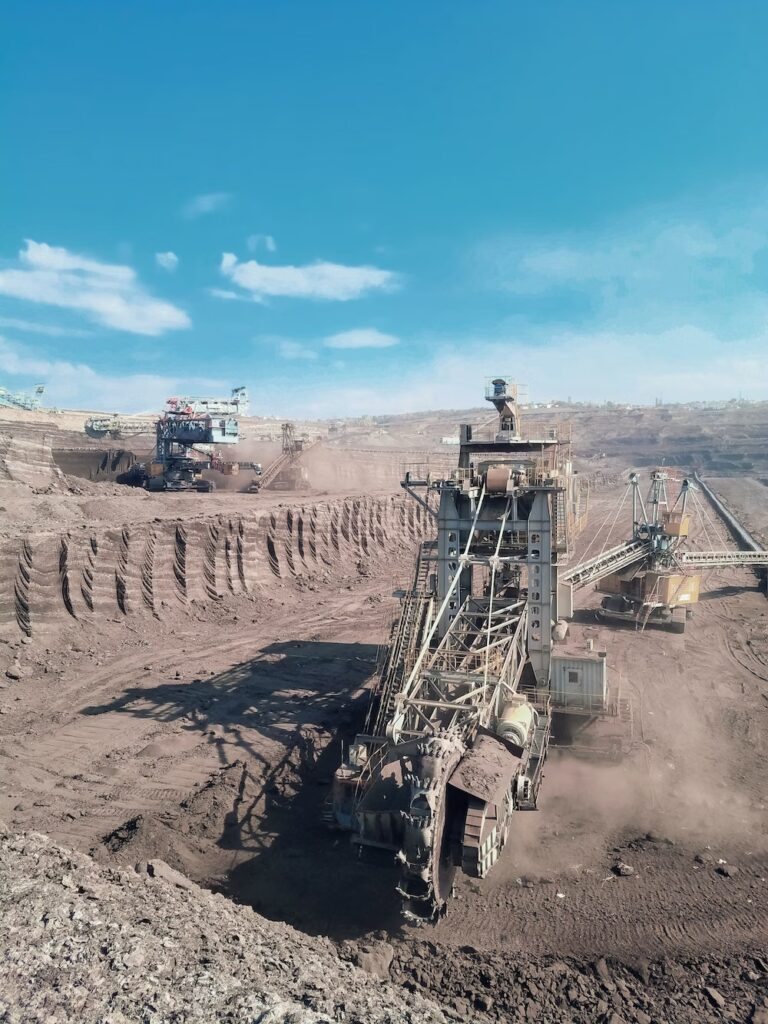
Profits and Challenges: The Dual Nature of Mining Firms
Mining companies operate in a dual nature, striving for profits while grappling with various challenges. The profitability of these organizations is closely tied to the prices of the commodities they extract, which can fluctuate significantly in response to market demand, geopolitical factors, and economic conditions.
Mining stocks are often influenced by the performance of the commodities market. When prices for metals like gold, silver, or copper rise, these organizations see an increase in revenue and profitability. Conversely, during downturns, they may face financial challenges and have to make strategic decisions to weather the storm.
Another challenge these organizations face is the depletion of mineral resources. As these resources are finite, firms must continually explore for new deposits and invest in exploration activities to secure their future operations.
Where They Operate: Global Footprints of Mining Giants
Mining organizations don’t limit their operations to a single region, instead, they cast a wide net, operating across continents to tap into diverse mineral resources. Here’s a glimpse into the global footprints of some of these giants.
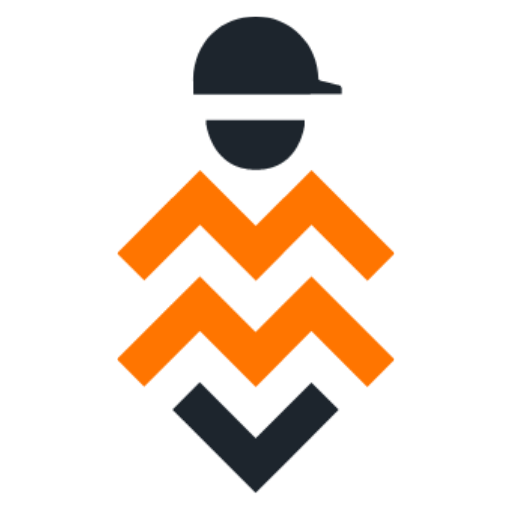
BHP Group
BHP Group operates in Australia, the Americas, and several other regions. This mining company is a significant contributor to the mining industry in Australia, particularly in iron ore production.
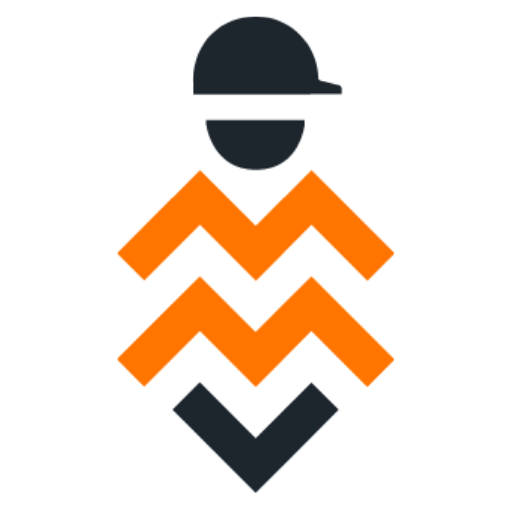
Rio Tinto
Rio Tinto’s operations span Australia, North America, Europe, and Asia. Its global presence ensures a steady supply of various resources to meet the demands of the market.
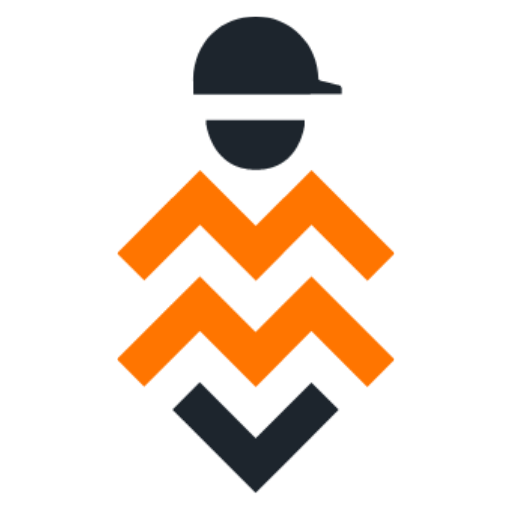
Cleveland-Cliffs
Cleveland-Cliffs primarily operates in North America, focusing on iron ore and metallurgical coal mining. Its proximity to steel mills in the region enhances its efficiency.
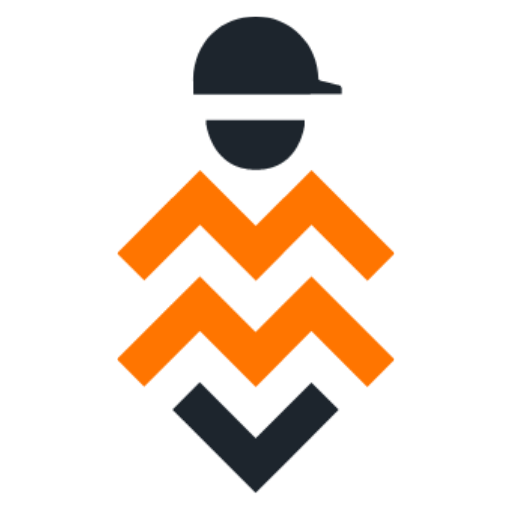
Anglo American
Anglo American has a diverse set of operations, with a presence in Africa, the Americas, Asia, and Australia. This broad reach allows it to extract a wide range of minerals.
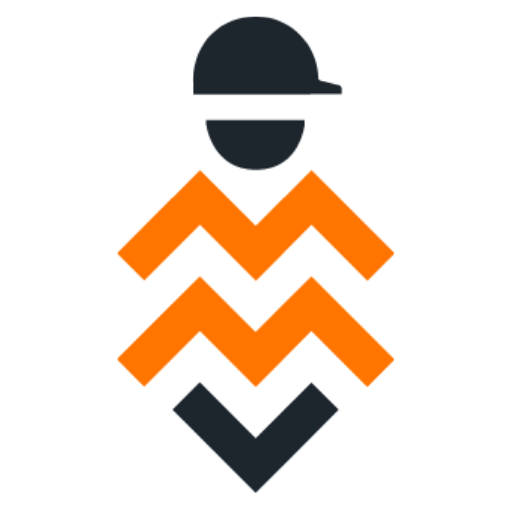
Glencore plc
Glencore plc has a vast global network, with operations in multiple countries. This allows it to trade and supply commodities worldwide, contributing to the global economy.
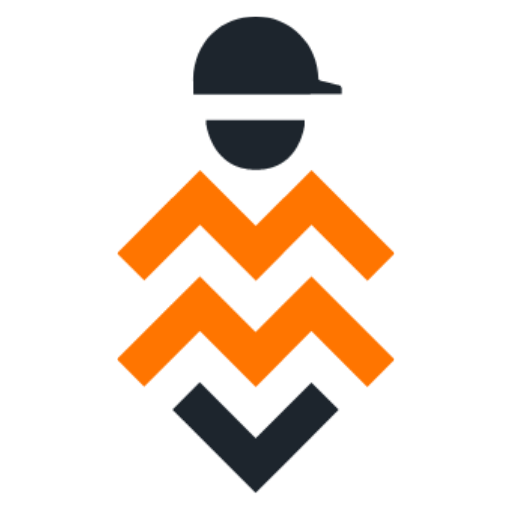
Gold Road Resources
After years of drilling and technical studies on its so-called “Gruyere” project, Gold Road now owns half of one of Australia’s biggest gold mines. Output is up 28%, costs down to $984 an ounce and its CEO has sold $244,531 at A$1.51.
The Future of the Industry: Innovations and Trends
The mining industry is not stagnant – it is constantly evolving in response to technological advancements, environmental concerns, and changing market dynamics. Several trends and innovations are shaping its future. In conclusion, mining companies are vital players in the global economy, extracting essential resources that fuel various industries. Their global operations, substantial market caps, and vast mining assets make them influential in financial markets. However, they also face the challenge of balancing profitability with sustainability, as responsible practices become increasingly important. With ongoing innovations and trends, the future of the sector promises to be marked by greater efficiency, sustainability, and responsible resource management. As the world’s appetite for minerals and metals continues to grow, these organizations will continue to play a crucial role in shaping our future.
Automation and Robotics
Mining operations are becoming increasingly automated, with the use of robotics, autonomous vehicles, and artificial intelligence. These technologies improve safety, efficiency, and productivity in mining activities.
Sustainable Practices
Sustainability will continue to be a focal point for organizations in this sector. The industry is exploring cleaner and more responsible mining practices, including reducing water usage, minimizing waste, and implementing renewable energy sources.
Battery Metals
The demand for battery metals such as lithium, cobalt, and nickel is expected to grow significantly due to the increasing adoption of electric vehicles and renewable energy storage. Organizations are positioning themselves to meet this demand.
Exploration in Untapped Regions
Mining firms are venturing into previously unexplored regions in search of new mineral resources. This includes deep-sea exploration for valuable minerals found on the ocean floor.
Digital Transformation
Digital technologies like blockchain and data analytics are being employed to enhance transparency in the supply chain, track the origin of minerals, and ensure ethical sourcing.
Green Mining
Green mining initiatives aim to reduce the environmental impact of mining activities through innovative technologies and processes. This includes recycling and reusing mining waste.